Electrically conductive adhesives are used in many different types of industries and applications. Some examples are electronics, solar cell, medical, aerospace, space and automotive applications.
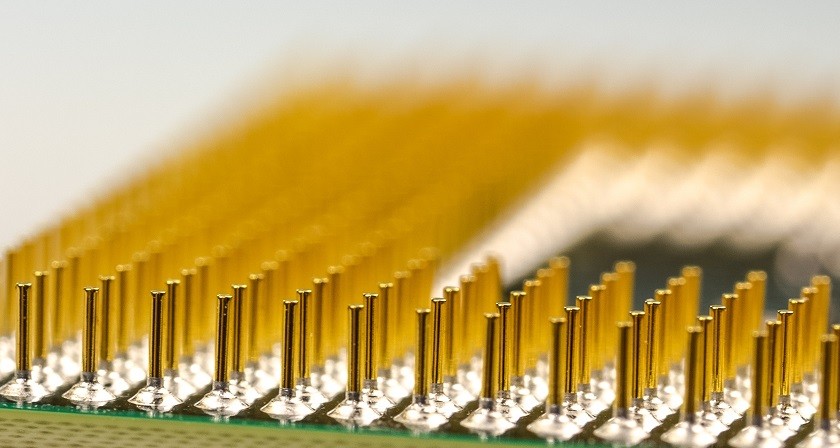
Why use an electrically conductive adhesive
An electrically conductive adhesive can be a good alternative in situations where for instance the components on a PCB cannot withstand soldering, or when electrical shielding is desired. The conductivity of the adhesive will determine the types of application in which it will be suited. The conductivity can vary depending on the type and amount of filler (“conductive” or “semi-conductive”). Volume resistivity [ohm·cm] is commonly the term, or property, used to describe the electrical conductivity of an adhesive. A lower volume resistivity implies a higher conductivity.
Tests have shown that electrically conductive silver-filled epoxy adhesives can replace soldering with equivalent results. There is basically no difference in conductivity or durability on AgPd components attached to a PCB, not immediately after curing of the adhesive or after many and long series of temperature cycling.
Sometimes, it is easy to get intimidated by the price of a silver-filled adhesive, but consider that usually much lower amounts of adhesive is consumed compared to solder in the same application.
Also in cases where a very high thermal conductivity is necessary, it is often suitable to choose an electrically conductive adhesive if there are no restrictions on electrical conductivity. Electrically conductive adhesives are also thermally conductive:
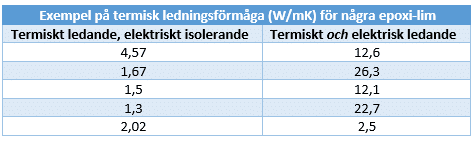
Electrically conductive adhesives can be dispensed, stamped or screen printed. Keep in mind that electrically conductive adhesives are not always compatible with tinned materials.
How can an adhesive be electrically conductive?
An adhesive base, which can be for example an epoxy or a silicone, can contain different filler materials. It is the filler material, and not the adhesive itself, which is electrically conductive.
The most common filler material for electrically conductive adhesives is silver (which is why this type of adhesive is often referred to simply as a ‘silver adhesive’). Other metal filler particles, such as nickel, copper or gold also exist, and carbon/graphite is also common. These fillers give different conductivities solely dependent on the filler material itself.
Different conductivities
The mechanism for the conductivity of an electrically conductive adhesive is the same regardless of filler. The filler particles must come in contact with one another to be able to create an electrical flow. So how do they do this? First and foremost, the adhesive manufacturer makes sure that the adhesive contains a high enough amount of filler. The rest is up to the user.
To enable the particles to interact, the adhesive must be cured properly. It is therefore important that the components of the adhesive are weighed in at the correct mix ratio, that they are mixed thoroughly and cured according to the specifications in the technical data sheet. There are both heat curing and room temperature curing electrically conductive adhesives.
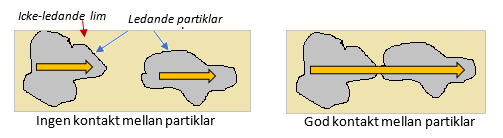
Curing at a higher temperature will for epoxies generally result in higher shrinkage. In the case of an electrically conductive adhesive, this is actually a good thing. The shrinkage pulls the filler particles together, leading to a higher conductivity. So if you are able to heat cure, it could be an advantage. However, you should also be careful not to cure at a too high temperature.
Apart from factors concerning the curing of the adhesive material, of course the type of filler will influence the conductivity. Silver has a higher conductivity than carbon for example. In some cases, static dissipative (“semi-conductive”) materials are just enough for an application where EMI- och RFI shielding is the purpose of them (Electromagnetic Interference och Radio Frequency Interference respectively) and a silver-filled material (which is more expensive than say, carbon) may not be necessary.
Environmental considerations
How a conductive adhesive is to be handled safely depends on the base of the product (and to some extent the filler). Please make sure to always consult the safety data sheet (MSDS) of the product before using it.
Product recommendations
Epo-Tek H20E (electrically conductive epoxy adhesive, heat curing, silver filled)
Epo-Tek EJ2189-LV (electrically conductive epoxy adhesive, room temperature curing)
Nusil R-1505 (electrically conductive silicone adhesive, 1K moisture cure, carbon-filled)
Nusil R-2631 (electrically conductive silicone adhesive, 2K)
Get in touch with us for advice on electrically conductive adhesives suitable for your application!